BlackBar Engineering’s Storm is coming to close military operational gaps
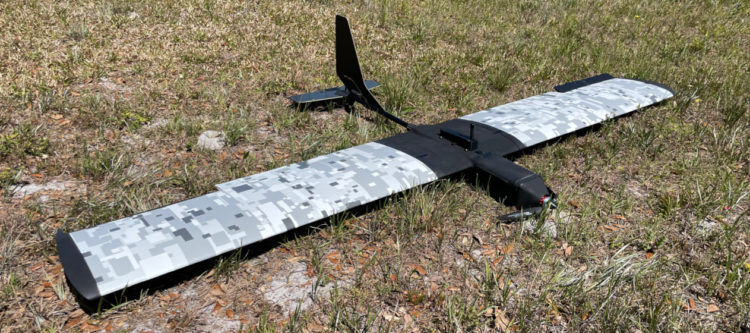
No matter how well prepared the U.S. military and its operators are for a mission, there is always potential for unforeseen challenges and complications. There are simply too many variables and environmental factors that can impact the mission and change requirements.
The unpredictable nature of warfighting makes flexibility and adaptability paramount to mission success. Unfortunately, many of the solutions and systems that are available to the warfighter are “one size fits all,” lack the modularity or adaptability to change with mission requirements, and leave operational gaps where they either can’t be used or aren’t ideal for the use case.
Closing these operational gaps is a large part of the mission for BlackBar Engineering, a small engineering firm that takes an innovative approach to product design, development, manufacturing, and testing. The company prides itself on rapidly prototyping and quickly introducing new solutions that can make tactical operators more effective.
We recently sat down with the firm’s CEO, Callie Groth, to get a better understanding of the company’s mission, and how its signature solution – the Storm unmanned aerial system (UAS) – is poised to drive increased mission success for military and law enforcement tactical operators.
The Last Mile (TLM): Can you tell our readers a bit about BlackBar Engineering? What does the company do? What products does it make, and who does it make them for?
Callie Groth: BlackBar is a small engineering firm. We specialize in the research, design, and development of autonomous vehicles, including both air and ground vehicles. We also specialize in the development of tactical tools and expeditionary equipment, which includes anything that fills a capability gap or an operational need. Everything that we develop helps to make a military operator or member of law enforcement lighter, faster, and more capable.
BlackBar was originally founded in 2015 and was renamed in 2018. But, since our inception, we have focused tirelessly on understanding our customers and their capability gaps and working to quickly design and develop solutions that fill those requirements.
Today, BlackBar does everything from ideation, concept design, CAD modeling, rapid prototyping, systems integration, testing, and analysis. We do small-scale fabrication and manufacturing so that we can keep everything as vertically integrated as possible. We also provide a complete testing capability through our test ranch – which is along the border between Arizona and Mexico, under restricted airspace.
This gives us the ability to identify an operational gap or requirement, come up with a solution, fabricate it, and test it. And we can do all of those things quickly since we can design and manufacture in-house and then walk out our back door to test it. In doing so, we can ensure that everything works and functions exactly as it would in an operational environment.
TLM: What is the Storm UAS? How is it different from other UAS solutions on the market?
Callie Groth: The Storm is a small Tactical Group I unmanned aircraft system. We began working on this aircraft in 2016 and later partnered with Naval Special Warfare Command under a cooperative agreement for research and development in 2018. The partnership was meant to help BlackBar further improve the system’s operational efficiency and effectiveness.
“Building the Storm with open systems and architecture meant that the operator has the ability to change things about the system – update firmware, update software, do whatever they need to do – so they can continue to operate in any environment.” – Callie Groth
The Storm is completely backpackable and can be transported, assembled, and operated by one person. It can also be assembled without tools or equipment. It was designed to make every process and operation factor as simple and easy as possible.
What really differentiates the Storm is its very small, tactical, and lightweight footprint. It’s easy for operators to carry and even easier for them to assemble – taking less than 10 minutes. The Storm can be assembled in the middle of the night by an operator wearing gloves. It can give them an “eye in the sky” in minutes. And it can be launched from virtually any position – including while crouched.
BlackBar is all about creating solutions to fill operations gaps and mission requirements that no other solution fills. We heard our military customers say that they had enough Group Two and Group Three unmanned aircraft. What they really needed was a smaller solution that could provide rapid, persistent reconnaissance.
The Storm is meant to be utilized by operational teams that quickly need to get a camera or sensor up in the sky, so they can have complete situational awareness.
TLM: What is special or unique about the way the Storm is designed? What considerations were taken when designing the Storm?
Callie Groth: When we first approached the design process, we looked closely at the requirements and what were the current accepted norms for the design and manufacturing of unmanned aircraft.
“We used to manufacture this aircraft in a very “old school” way. We would spend hundreds of thousands of dollars and lots of time – often eight to ten weeks – machining molds…This was not ideal for a number of reasons.” – Callie Groth
We began to analyze the design of the aircraft – how it would be packaged, how it would come out of the package, and the way it would assemble. This led us to reevaluate the best ways to connect different parts of an aircraft. Without changing the airframe or the structure of the aircraft, we were looking for and identifying ways to make things come together more seamlessly and without the need for tools.
Next, we began to think about materials. We asked ourselves how we could change the materials that were traditionally used in aerospace and aircraft manufacturing to make this system better for the operator. And, to accomplish this, we started evaluating materials that were not necessarily specific to aerospace, but were widely used in other industries like automotive, outdoor equipment, and others.
We also took a hard look at the system. One of the biggest requirements that came out of Naval Special Warfare was to make this an open architecture system.
“Everything that we develop helps to make a military operator or member of law enforcement lighter, faster, and more capable.” – Callie Groth
Building the Storm with open systems and architecture meant that the operator has the ability to change things about the system – update firmware, update software, do whatever they need to do – so they can continue to operate in any environment. To accomplish this, we worked to leverage commercial-off-the-shelf (COTS) components that can be purchased from various vendors if the military needs to quickly fix, repair, or replace parts.
TLM: How do all of these considerations – and the subsequent design decisions – end up making the Storm unique and different from other unmanned aerial systems on the market?
Callie Groth: Understanding that the military wants reliable, assured systems that will just work when they’re needed, we reevaluated how to manufacture these unmanned aircraft, and what to manufacture them with. We used to manufacture this aircraft in a very “old school” way. We would spend hundreds of thousands of dollars and lots of time – often eight to ten weeks – machining molds. We would then use those molds to manufacture the Storm’s individual parts out of either fiberglass or carbon fiber. These are the materials that are traditionally used in the manufacturing of aircraft.
This was not ideal for a number of reasons. First, there are added financial and human capital expenses to this process. The molds are expensive to produce, and their creation is a bottleneck in the manufacturing process. Then, the carbon fiber or fiberglass that was being used would create operational challenges that impacted the military’s ability to easily repair the aircraft.
“BlackBar does everything from ideation, concept design, CAD modeling, rapid prototyping, systems integration, testing, and analysis.” – Callie Groth
Should an unmanned aircraft crash or sustain damage, the traditional materials that are used to manufacture them have a tendency to splinter and shatter. To fix this problem, we evaluated materials from other industries – materials such as nylons, plastics, and 3d printable composites – that have the same structural rigidity and tensile strength as carbon fiber or fiberglass. These materials are just as strong, but they’re more forgivable and easier to fix should the aircraft be damaged in the field.
This change in how we manufacture the Storm has also helped to make the system more adaptable to different military operating environments and mission requirements. Our end users often find that a “one size fits all” solution can’t meet all mission requirements. They need the ability to adapt to the needs and parameters of the mission. Maybe they need to fly one mission that requires a camera payload but then need to fly another mission that requires an electronic warfare payload.
To meet this requirement, we designed a platform that is much more modular. We then embraced 3d printing to help make the manufacturing process more adaptable to mission requirements. If we need to make any changes to this airframe – if we need to add different mount points or change the size of the payload bay to accommodate something that has different dimensions than what is currently configured – we can do that in a matter of hours. We’re not bound by the large-scale molds that make changes both cost and time prohibitive.
To learn more about BlackBar Engineering and its Storm UAS solution, click HERE.
Disclaimer: Please note, for all aerial assets, be sure to follow any applicable government regulations and restrictions during your deployment.
No Comment